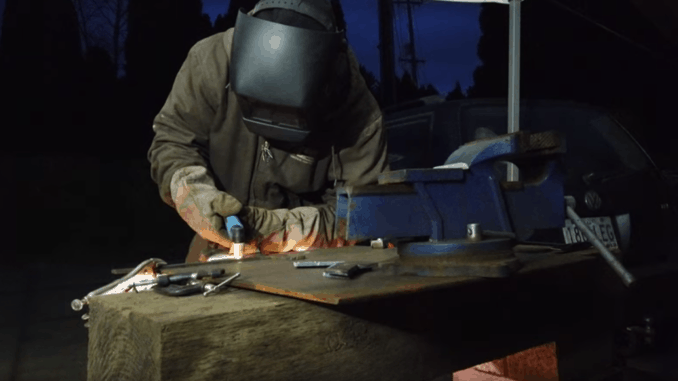
Those familiar with inverters usually know they offer size, weight, and portability advantages. They also can improve reliability by overcoming primary power fluctuations, also known as dirty power.
Question: Does the weight of the plasma cutter matter?
Answer: Yes, because labor accounts for about 85 percent of a fabricated product’s cost.
An inverter-based plasma cutter that cuts gauge-thickness through about 1/2-inch material—the largest segment of the plasma cutting market—weighs three or four times less than a conventional machine. One or two people can carry a unit around a job site or shop, and it takes up little space on a service truck.
An inverter-based plasma cutter that cuts gauge-thickness through about 1/2-inch material—the largest segment of the plasma cutting market—weighs three or four times less than a conventional machine. One or two people can carry a unit around a job site or shop, and it takes up little space on a service truck.
Q: Why are inverter-based plasma cutters so light?
A: It has to do with the way they convert primary power to output power.
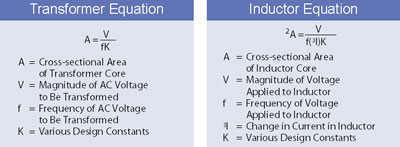
A power source accomplishes this job through its transformer and inductor, both of which comprise copper wire windings around a metal core, the heaviest components of a power source. Certain variables determine the size of the transformer and inductor, and these are controlled by the variables in the equations shown in Figure 1.
However, the number of wire turns and area of the core are inversely proportional to frequency. Traditional plasma cutters use 60-Hz-frequency primary power, so they need a massive transformer and inductor. That’s why a conventional plasma machine with a 1/2-in. cut rating weighs about 150 lbs.
Rated cut is the thickness of mild steel that can be cut with good cut quality at a rate of 10 inches per minute (IPM) using a hand-held torch. Thicker metal may be cut, but at slower speeds or with reduced cut quality.
Q: How does an inverter power source create its own operating frequency?
A: With power-switching semiconductors.
These semiconductors switch primary power on and off rapidly (tens of thousands of times per second) to create high-frequency AC power for the transformer (see Figure 2).
Inverter-based machines create their own operating frequency, tens of thousands of hertz. This design principle enables engineers to use a smaller transformer and inductor. As a result, an inverter-based plasma cutter with a 1/2-in. rated cut weighs about 55 lbs.
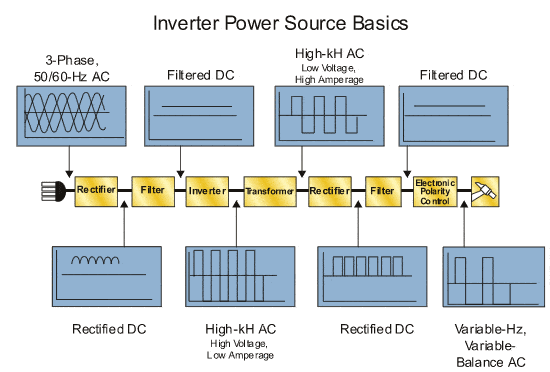
Q: Does switching speed offer other advantages?
A: Yes, especially relating to primary power fluctuations.
Irregularities in primary power—such as voltage spikes and dips, also known as dirty power or line notching—are reflected in the cutting output of a conventional machine. However, inverter speed is faster than the speed of these irregularities and compensates for them. The result is smooth, consistent cutting and less rework. Symptoms of improperly managed primary power include rough edges, excess slag, and the inability to cut at rated capacity.
Q: What is line voltage compensation?
A: It’s a machine’s ability to manage primary power fluctuations to maintain a steady output.
For example, a machine with line voltage compensation running off 230-volt primary power can maintain a steady arc even if primary power fluctuates by 10 percent or more. Some machines can maintain a steady arc with fluctuations between 176 and 264 V.
Q: What types of primary power does an inverter use?
A: Many different types, without any manual adjustment.
Conventional machines require different designs for single- or three-phase power and 50- or 60-Hz power, and they need to be relinked manually for different primary power voltages. However, because an inverter creates its own power, it can be plugged in almost anywhere.
Q: Do inverter-based plasma cutters require a larger circuit breaker?
A: No.
Inverters have power factor correction (PFC), which helps ensure that every available amp of primary power is converted into usable cutting power. For example, a plasma cutter in the 1/2-in. class with PFC draws about 30 primary amps on a 230-V line, or about 30 percent less than a machine without PFC.
Q: Do inverters perform well off generator power?
A: Those with PFC do.
PFC is especially useful with generator power because, on some engine drives, the generator power produced isn’t voltage-regulated and the voltage tends to droop; long extension cords further exacerbate the situation. As a result, plasma cutters without PFC demand more amperage and are more likely to trip the circuit breaker.
In addition, several manufacturers engineer their plasma cutters to ensure that the machines cut close to their rated capacity when running off generator power. Plasma cutters gained a bad reputation in the field because some machines couldn’t cut more than 3/8 in., even though they were rated for much thicker metal. This is not true of all machines.
If you plan to operate a plasma cutter off generator power, be sure to test the entire system before making a purchase. The cutting quality with generator power varies greatly. As a side note, be sure to rewire the plug when switching between generator power and wall power.
Q: Can inverter-based plasma cutters withstand tough conditions?
A: Those with the right reliability features can.
Among the key features to look for are technologies that can isolate sensitive electronics from the cooling airflow —you should be able to see through the hollow tunnel of the machine—and minimize the amount of airborne particles pulled into the machine by turning on the cooling fan only when needed.
Q: Do all inverter-based plasma cutters use high frequency to start or maintain the arc?
A: No.
The machines that don’t use high frequency for arc starting have an electronic pilot arc controller. After arc start, this feature boosts pilot current only when needed for a strong arc transfer, which extends tip life. It also automatically reignites the pilot arc while cutting grates, chain link fence, and other expanded and perforated metals.
Shop for inexpensive inverter-based plasma cutters Amazon.
From: thefabricator.com